The crankshaft of a compressor is a crucial component that converts the linear motion of the pistons into rotational motion, or vice versa, depending on the type of compressor. It plays a fundamental role in the operation of reciprocating compressors, which are widely used in various applications to compress gases.
Crankshafts in reciprocating compressors also have a certain amount of end play, or thrust, which allows them to "float" axially to prevent excessive bearing wear. The amount of thrust is determined by the machine's OEM, and it should be set when new compressor skids are made, engines are "swung", or crankshafts or bearings are replaced during maintenance. Incorrect thrust settings can affect the quality of shaft alignment results.
Functions of the Crankshaft
Converting Motion:
The primary function of the crankshaft is to convert the reciprocating (linear) motion of the pistons into rotational motion. This conversion is essential for the compressor to function correctly, enabling the continuous compression of gas.
Driving the Pistons:
In a reciprocating compressor, the crankshaft drives the pistons through connecting rods. As the crankshaft rotates, it causes the pistons to move up and down within their respective cylinders, compressing the gas.
Balancing the System:
The crankshaft is designed to balance the forces generated by the reciprocating motion of the pistons. This balance helps to minimize vibrations and ensures smooth operation of the compressor.
Design and Components
Main Journals:
These are the portions of the crankshaft that rotate within the main bearings. The main journals support the crankshaft within the compressor housing and allow it to rotate smoothly.
Crankpins (Rod Journals):
Crankpins are offset from the main journals and are the points where the connecting rods attach to the crankshaft. The offset design is what allows the conversion of linear piston motion to rotational motion.
Counterweights:
To balance the crankshaft and reduce vibrations, counterweights are often incorporated. These are strategically placed to counteract the forces created by the moving pistons.
Thrust Bearings:
Thrust bearings are sometimes integrated into the crankshaft assembly to handle axial loads and keep the crankshaft in proper alignment.
Types of Crankshafts
Single-Piece Crankshaft:
Typically used in smaller compressors, a single-piece crankshaft is manufactured as a single unit. It is simpler in design and easier to manufacture but may have limitations in terms of strength and size.
Built-Up Crankshaft:
Used in larger compressors, a built-up crankshaft consists of multiple components assembled together. This design allows for greater strength and can be tailored to specific requirements of larger and more powerful compressors.
Materials
Crankshafts are generally made from high-strength materials to withstand the stresses and forces during operation. Common materials include:
Forged Steel: Known for its strength and durability, forged steel crankshafts are common in heavy-duty applications.
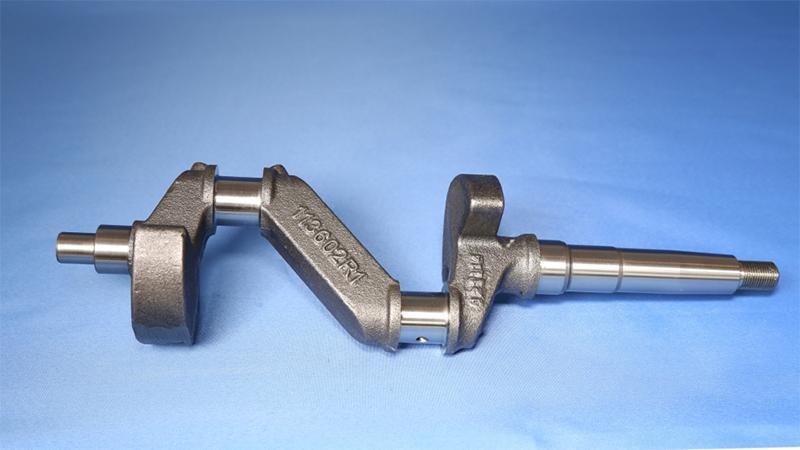
Cast Iron: Used in less demanding applications, cast iron is a cost-effective material with good wear resistance.
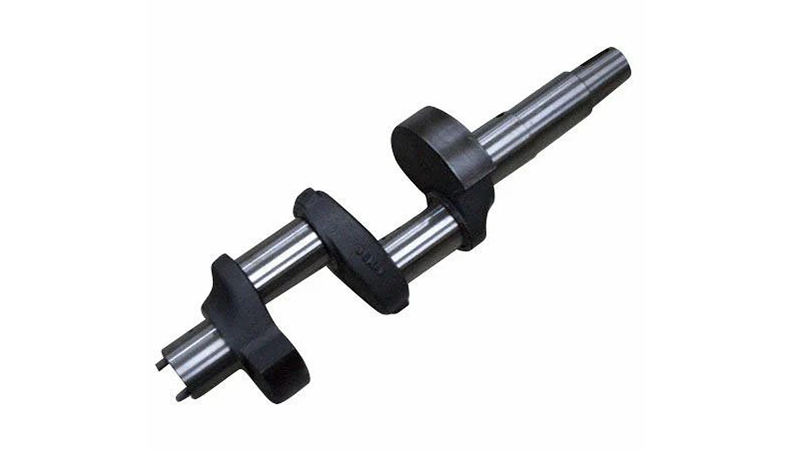
Alloy Steels: These provide a good balance between strength, toughness, and resistance to wear and fatigue.
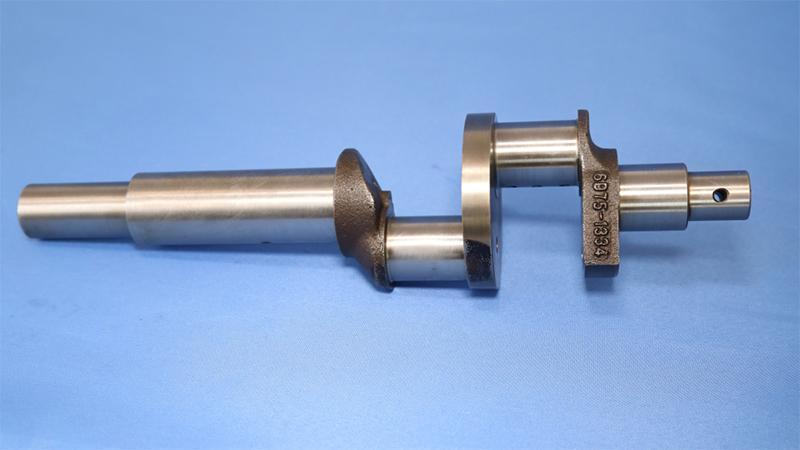
Maintenance and Issues
Regular inspection and maintenance of the crankshaft are essential to ensure the reliable operation of the compressor. Common issues that may arise with crankshafts include:
Wear and Tear: Over time, the crankshaft can experience wear at the journals and crankpins, leading to loss of efficiency and potential failure.
Fatigue Cracks: Repeated stress cycles can lead to the formation of cracks, which may eventually cause the crankshaft to fail.
Imbalance: An imbalanced crankshaft can lead to excessive vibrations, causing damage to other components and reducing the overall lifespan of the compressor.
To mitigate these issues, regular maintenance practices include:
Lubrication: Ensuring proper lubrication to reduce friction and wear.
Inspection: Regular inspection for signs of wear, cracks, and other damage.
Balancing: Periodic balancing to ensure smooth operation and reduce vibrations.
In summary, the reciprocating compressor crankshaft is a vital component that facilitates the conversion of reciprocating motion to rotational motion, driving the pistons and ensuring efficient gas compression. Its design, material selection, and maintenance are crucial for the reliable operation and longevity of the compressor.