A reciprocating compressor works by using a piston within a cylinder to compress gas and increase its pressure. This type of compressor is commonly used in various industrial applications due to its ability to produce high-pressure gas efficiently. Here’s a detailed explanation of how a reciprocating compressor operates:
Basic Components
Cylinder: The chamber where gas compression occurs.
Piston: Moves back and forth within the cylinder to compress the gas.
Crankshaft: Converts rotational motion into the reciprocating motion of the piston.
Connecting Rod: Links the piston to the crankshaft.
Valves: Control the flow of gas into and out of the cylinder. These include suction (inlet) and discharge (outlet) valves.
Crosshead: Guides the piston rod and reduces side loads on the piston.
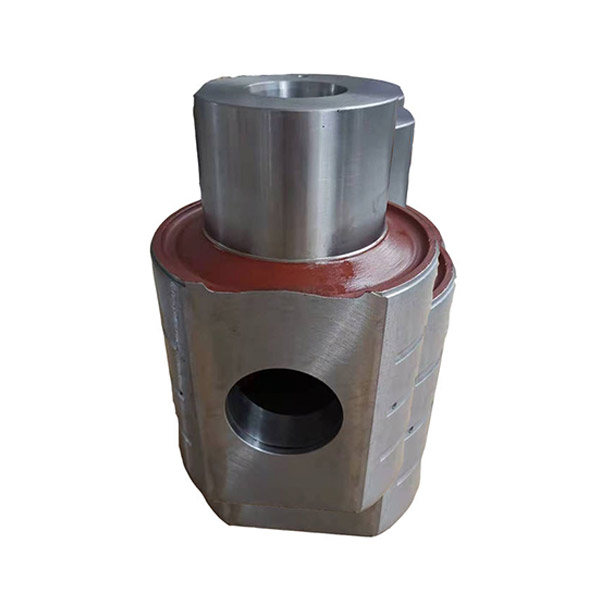
Flywheel: Helps maintain the rotational motion of the crankshaft.
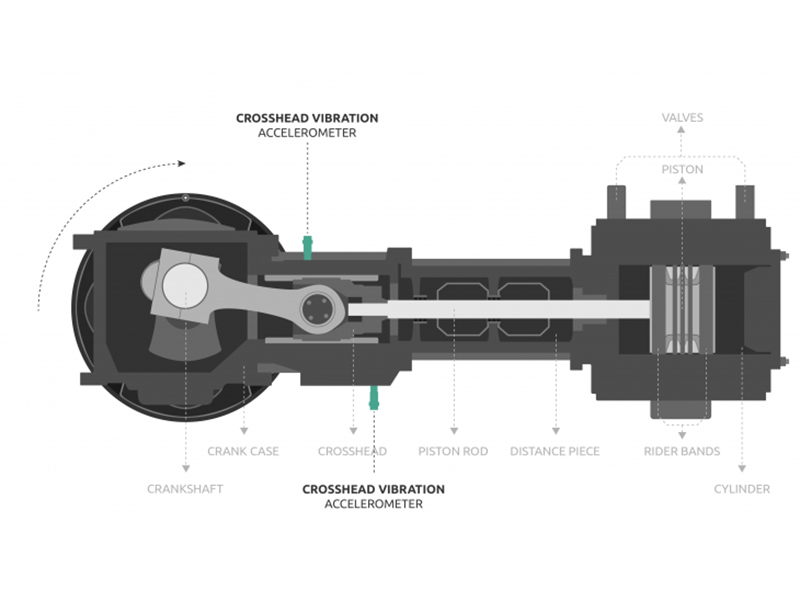
Operating Cycle
The operation of a reciprocating compressor involves four main stages: intake, compression, discharge, and exhaust. Let’s break down each stage:
Intake Stroke (Suction):
- The piston moves downwards, creating a vacuum in the cylinder.
- The suction valve opens, allowing gas to flow into the cylinder from the intake manifold.
- The discharge valve remains closed.
Compression Stroke:
- The piston moves upwards, compressing the gas within the cylinder.
- The suction valve closes to prevent the gas from escaping back into the intake manifold.
- The pressure of the gas increases as the volume decreases.
Discharge Stroke:
- As the piston reaches the top of its stroke, the pressure inside the cylinder exceeds the pressure on the discharge side.
- The discharge valve opens, allowing the compressed gas to flow out of the cylinder into the discharge manifold.
- The suction valve remains closed during this phase.
Exhaust Stroke:
- The piston moves down again, and the discharge valve closes.
- Any remaining gas in the cylinder is expelled, preparing the cylinder for the next intake stroke.
Key Features and Considerations
Compression Ratio:
The ratio of the volume of gas before compression to the volume after compression. Higher compression ratios result in higher pressure gas.
Cooling:
Compression generates heat, so compressors often have cooling systems (water or air-cooled) to dissipate heat and prevent overheating.
Lubrication:
Proper lubrication is necessary to reduce friction and wear between moving parts. Lubrication systems ensure that components like pistons, connecting rods, and crossheads operate smoothly.
Staging:
Multi-stage compressors use multiple cylinders with different sizes to achieve higher pressures. In each stage, the gas is partially compressed, then cooled, and then further compressed in the next stage.
Unloading Mechanisms:
To control the compressor load, unloading mechanisms like suction valve unloaders, bypass valves, or variable speed drives can be used. These mechanisms help in reducing the energy consumption and wear on the compressor during periods of low demand.
Advantages and Applications
Advantages:
- Ability to achieve high pressures.
- Suitable for a wide range of gases.
- Reliable and well-understood technology.
- Scalable from small to very large capacities.
Applications:
- Industrial processes (chemical plants, refineries).
- Natural gas processing and transportation.
- Refrigeration and air conditioning systems.
- Power plants.
- Pneumatic tools and systems.
Conclusion
A reciprocating compressor functions by using the reciprocating motion of a piston to compress gas within a cylinder. The process involves intake, compression, discharge, and exhaust stages, facilitated by the coordinated actions of pistons, valves, crankshafts, and connecting rods. With its ability to achieve high pressures and its versatility across various applications, the reciprocating compressor remains a fundamental component in many industrial processes. Proper cooling, lubrication, and load management are essential to ensure its efficient and reliable operation.