Compressor valves are crucial components in reciprocating compressors, regulating the flow of gas into and out of the compression chamber. They operate automatically in response to pressure differences and are designed to open and close at precise times during the piston's movement. Here's an in-depth look at how compressor valves work:
Types of Compressor Valves
Suction (Inlet) Valve:
Allows gas to enter the cylinder from the intake manifold during the intake stroke.
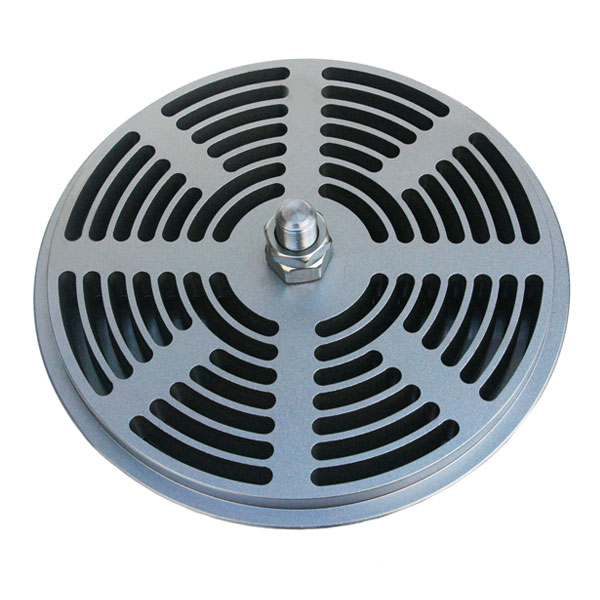
Discharge (Outlet) Valve:
Allows compressed gas to exit the cylinder into the discharge manifold during the discharge stroke.
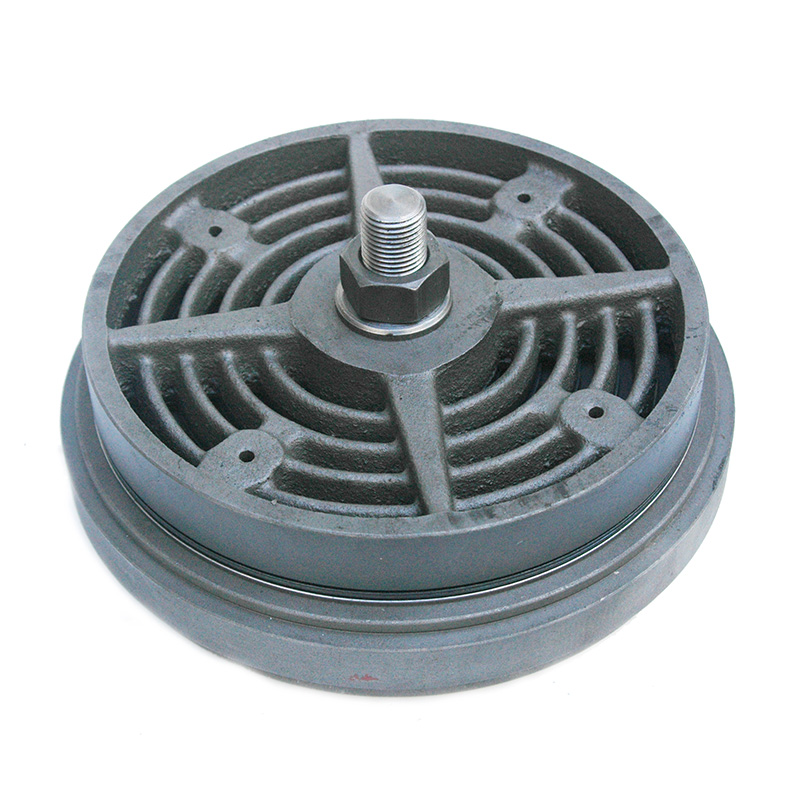
Basic Operation Principles
Compressor valves operate based on pressure differentials across the valve plate. They open and close automatically as the piston moves through its strokes. Here’s a step-by-step breakdown of their operation during a complete cycle of a reciprocating compressor:
Intake Stroke:
Piston Movement: The piston moves downwards, increasing the volume in the cylinder.
Pressure Differential: The pressure inside the cylinder drops below the pressure in the intake manifold.
Suction Valve Action: This pressure differential causes the suction valve to open, allowing gas to flow into the cylinder from the intake manifold.
Discharge Valve: The discharge valve remains closed due to the lower pressure in the cylinder compared to the discharge manifold.
Compression Stroke:
Piston Movement: The piston moves upwards, decreasing the volume in the cylinder.
Pressure Differential: The pressure inside the cylinder increases as the gas is compressed.
Suction Valve Action: As the pressure in the cylinder rises above the pressure in the intake manifold, the suction valve closes, preventing backflow of gas.
Discharge Valve: The discharge valve remains closed until the pressure in the cylinder exceeds the pressure in the discharge manifold.
Discharge Stroke:
Piston Movement: The piston continues to move upwards.
Pressure Differential: The pressure in the cylinder becomes higher than the pressure in the discharge manifold.
Discharge Valve Action: This pressure differential causes the discharge valve to open, allowing the compressed gas to flow out of the cylinder and into the discharge manifold.
Suction Valve: The suction valve remains closed during this phase.
Exhaust Stroke:
Piston Movement: The piston moves downwards again.
Pressure Differential: The pressure inside the cylinder drops as the volume increases.
Discharge Valve Action: The discharge valve closes once the pressure in the cylinder drops below the pressure in the discharge manifold.
Suction Valve: The cycle repeats with the suction valve opening again when the pressure in the cylinder drops below the intake pressure.
Valve Design and Components
Valve Plate:
The main body of the valve where the sealing elements and springs are mounted. It is typically made from durable materials like stainless steel or other high-strength alloys to withstand high pressures and temperatures.
Sealing Elements:
These could be rings, discs, or other shapes that seal against the valve seat to prevent gas flow. They open and close in response to pressure differentials.
Springs:
Springs are used to keep the sealing elements in the closed position when there is no pressure differential. They ensure that the valves open and close at the correct times by providing the necessary resistance.
Valve Seat:
The surface against which the sealing element rests to create a seal when the valve is closed.
Valve Guard:
A protective structure that holds the sealing elements and springs in place and prevents them from excessive movement or damage.
Maintenance and Troubleshooting
Compressor valves are subject to wear and tear due to the high pressures and temperatures they experience. Regular maintenance is essential to ensure their proper functioning. Common issues include:
Wear and Tear: Sealing elements and springs can wear out over time, leading to leaks or inefficient operation.
Contamination: Dirt and debris can cause valves to stick or not seal properly.
Fatigue: Repeated cycling can cause metal fatigue in the valve components, leading to failure.
Conclusion
Compressor valves are essential for regulating the flow of gas in reciprocating compressors. They operate automatically based on pressure differentials created by the piston's movement, ensuring that gas enters and exits the compression chamber at the correct times. Proper design, material selection, and regular maintenance are crucial for the efficient and reliable operation of compressor valves.